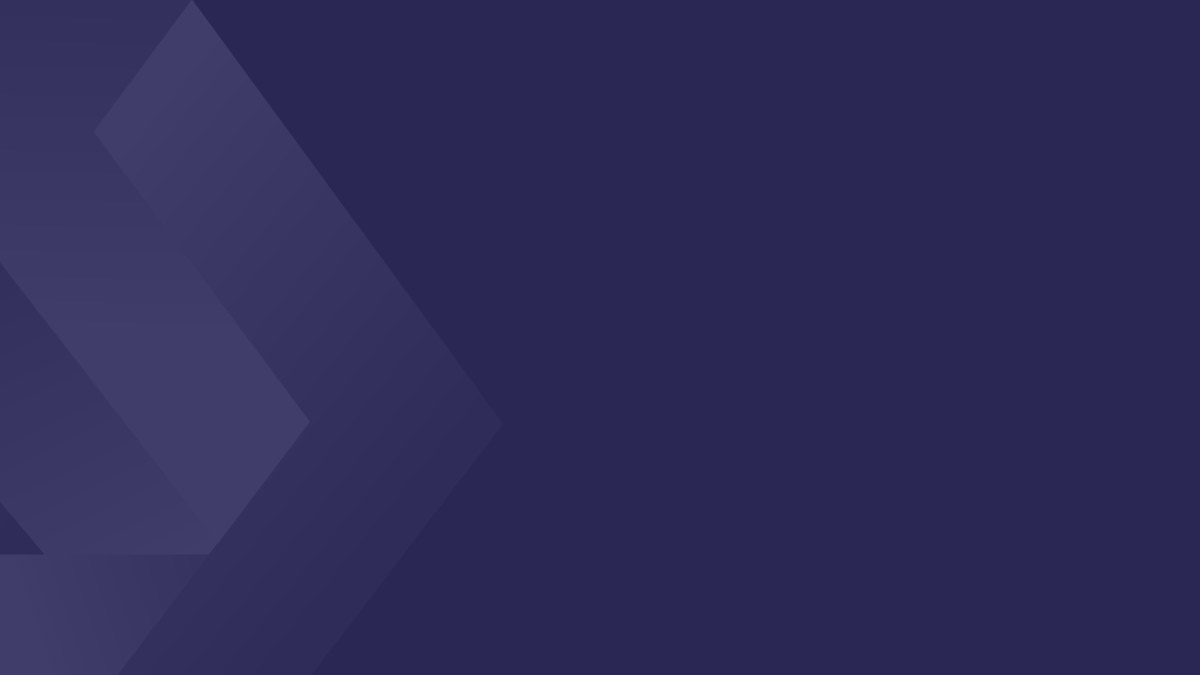
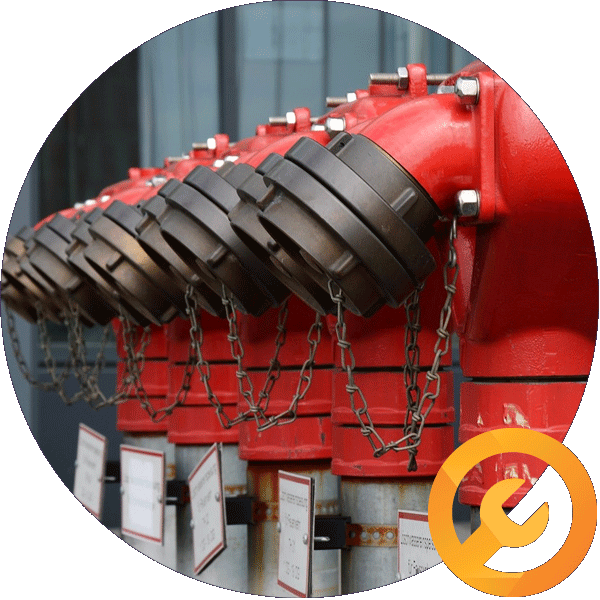
Service
Hydrants
By law in the state of Victoria, hydrants have to be tested on regular basis, this ensures that when an emergency arises the system is capable of operating and performing as it should.
Even though a hydrant system is designed and installed to protect that building, doesn’t mean in the coming years the system will still be able perform as it was first installed. Corrosion of internal components such as rubber washers will affect the backflow prevention of the hydrant system, couplings for support, also an increase in water demands in the area over time will affect the flow rate of a system, which will affect the performance.
Other services
Six-monthly test
6-monthly hydrant test is conducted in accordance with AS1851-2012 table 4.4.2.
Basically, every six months the hydrant is visually inspected and proof of water flow is conducted at every hydrant to indicate it is still operating sufficiently and the mechanism of the internal components are in good working order in case of an emergency.
The same test is conducted for fire hose reels to ensure there are also in good operating order.
The hydrants is then tagged to indicate it has been tested and a report is produced for record keeping.
Annual flow test
A yearly service schedule fire hydrant system is also recognised as an annual flow test, tested in accordance with AS1851-2012 4.4.3.
This service tests the most disadvantage hydrant on site from the water tapping to the property and a visual inspection and flow test is conducted.
The flow test is calculated in KPA and converted into litres per second to indicate if there is sufficient flow for emergency use.
The result will yield a report which is kept for record keeping.
The hydrant is then tagged to indicate it has been tested and a report is produced for record keeping.
3-yearly flow test
This test is conducted every 3 years in accordance with AS1851.4-1992 which test the flow rate and static pressure in the mains from the most disadvantage hydrants from the mains tapping. A pump appliance test is also conducted using a fire pump to test the friction loss of the system and the working pressure.
A visual inspection and a report is produce on completion for record keeping.
The hydrants are then tagged to indicate they have been tested and a report is produced for record keeping.
5-yearly flow test
A 5-yearly service of the hydrant system is conducted in accordance with AS1851-2012 4.4.4.
This test is carried out every 5 years is and considered a major test to inspect the integrity of the hydrant system andt to see if the system has sufficient flows to extinguish a fire in an emergency.
A flow test is carried out and calculated in KPA and converted in litres per second. This will give an indication if it still meets the minimum flow test required by Australian Standards. Afterwards, a pump appliance test is carried out to calculate the friction loss of the system and the working pressure. This will establish if the system is safe to operate under emergency conditions.
Finally, a pressure test is carried out to check the integrity of the mains for any leaks, given over time the ground movements which can affect the integrity of the mains. This test will also give an indication if the check valve is operating sufficiently in regards to backflow prevention.
Hydrants are then tagged to indicate they have been tested and a report is produced for record keeping.
6-yearly flow test
A 6-yearly service of the hydrant system is conducted in accordance with AS1851.4 1992.
This test is carried out every 6 years, primarily on building built before 2005, and considered a major test to inspect the integrity of the hydrant system. A test is also conducted to see if the system has sufficient flows to extinguish a fire in an emergency.
A flow test is carried out and calculated in KPA and converted in litres per second. This gives an indication if the hydrant still meets the minimum flow test required by Australian Standards. Afterwards, a pump appliance test is carried out to calculate the friction loss of the system and the working pressure. This will establish if the system is safe to operate under emergency conditions.
Finally, a pressure test is carried out to check the integrity of the mains for any leaks, given over time the ground movements which can affect the integrity of the mains. This test will also give an indication if the check valve is operating sufficiently in regards to backflow prevention.
Hydrants are then tagged to indicate they have been tested and a report is produced for record keeping.
Regulation 309 Consent
In accordance with regulation 109 of the Building Regulations 2006, the Building Code of Australia (BCA) is adopted by and forms part of the regulations. The BCA sets the minimum requirements for building construction. In accordance with regulation 309 of the Building Regulations 2006, if any of the following prescribed fire safety matters do not meet the deemed-to-satisfy provisions of the BCA (i.e. are proposed to be less than the minimum requirements) the Consent of the Chief Officer must be obtained prior to a Building Permit being issued.
- Fire hydrants
- Fire hose reels
- Fire control centers or fire control rooms
- fire precautions during constructions
- Fire mains
- Control valves
- Booster assemblies
- Emergency vehicle access
- Fire indicator panels (FIP)
- Proscenium curtain drencher systems
- Fire services controls in passenger lift cars
It should be noted that the Chief Officer is not obligated to Consent and Delegated Officers in CFA Region offices assess each application on its merits.
Get started today!
Contact us today for a free, no-obligation quote to service, install or commission your fire safety system.